RECOMMENDATIONS
1. Warnings
regarding lid opening hazards must be prominently displayed on
or about any pressure vessel. Adhesive backed warning
labels are available through the Gaston County Dyeing Machine
Company Parts Department by calling 704-822-5000. Part
numbers and wording are shown below:
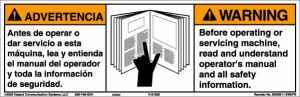
FREE UPON REQUEST - Adhesive
Label (8.3" 2.7")
Part number 4121608
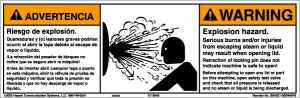
FREE UPON REQUEST - Adhesive
Label (8.3" 2.7")
Part number 9119048
NOTE: Due to the
harsh environment associated with dyeing and bleaching
equipment, warning plates and labels may deteriorate over time
and require periodic replacement. For proper application
instructions, refer to "Application Procedures for Pressure
Sensitive Adhesive Backed Labels & Plates."
2. All vessels having a
Quick Lock lid (manual or automatic) should have an automatic
vent valve by which the vessel may be freely vented to
atmosphere as a prerequisite to opening the lid. As an
additional safety interlock, the air supply to the solenoid
which retracts the toggle locking pin should be derived from the
vent signal air such that the toggle pin cannot be retracted
without the automatic vent having first been opened.
3. All vessels having a
Quick Lock lid with manually operated toggle must have an Interlocking
Manual Safety Test Valve Assembly by which the machine
operator is required to check for discharge of pressure, steam,
or liquid before the vessel lid can be unlocked. An
integral limit switch interlock requires the test valve to first
be opened before the toggle pin can be retracted. The test
valve must have an open discharge to give audible and/or visual
indication to the operator if the vessel is pressurized or has
hot liquor above the valve level. The bore of the valve
must be large enough (typically 1/2 inch) to avoid blockage.
For vertical pressure vessels, the Test Valve Assembly must be
situated below the vessel lid. For horizontal vessels, the
Test Valve will be mounted to the side of the vessel and
an additional interlock provided to insure the machine is fully
drained before retracting the toggle pin to allow opening the
lid.
4. Some older machines
utilized a Gaston County manufactured pressure switch as the
primary interlock for the toggle locking pin. Any Gaston
County manufactured pressure switches should be replaced with a
new Static-O-Ring pressure switch (Gaston County part number
7759509) set for 4 inches of water column.
5. Interlock systems for
quick lock lids must include an auxiliary safety pressure
sensing device set for 4 psi or less to prevent operation of all
atmospheric functions and the toggle licking pin above the set
pressure. Note: This safety pressure sensor is in
addition to the Static-O-Ring pressure switch which serves as
the primary interlock for the locking pin.
6. Interlock systems for
quick lock lids must include a temperature sensing device set
for 200 degrees F or less to prevent operation of the toggle
locking pin above the set temperature. The sensor must be
configured for "fail safe" operation to a high
temperature condition.
7. Gauges may be installed
on pressure vessels to provide visual indication of a
pressurized condition. However, due to the relatively high
pressure range (0-100 psi) required for most dyeing and
bleaching applications, gauge resolution and readability may not
provide a reliable indication of pressure on the lower end of
the scale. Like other sensing devices, gauges are also
subject to calibration error and failure. While gauge
readings can be used to indicate the presence of pressure within
a vessel, the gauge alone must not be relied upon to indicate
the absence of pressure or to indicate that a machine is safe
for opening.
8. Each plant must develop
written procedures, instructions, and training for the safe
operation of machines having Quick Lock Lids. This
includes use of a test valve to verify no steam, pressure or
liquid discharge prior to opening. Operators must be
provided with suitable protective gear, especially where
"in bath sampling" is utilized, and training in its
use. Required equipment may include such items as face
shield, body apron, boots, gloves, etc. Adherence to
procedures and use of protective equipment must be strictly
enforced.
9. Quick Lock systems are
subject to failure and require regularly scheduled inspection
and preventive maintenance at least monthly - more often where
experience dictates or problems are suspected. Refer to
"Gaston County's Safety Inspection Check List" for
further recommendations and procedures. Particular
attention should be given to operation of the Static-O-Ring
pressure switch which is a vital part of the interlock system.
This switch is factory pre-set at 4 inches of water column and
should never be field adjusted or repaired. Any switch
that fails to meet the specification outlined in the
aforementioned check list or fails to operate correctly should
be replaced with a new switch of the same type - no substitutes
permitted.
10. Machines found to have
defective Quick Lock systems should be removed from operation
until repairs can be made. Under no circumstances should
components be removed, substituted, defeated or altered in any
way.
11. Machine operators
should be trained to assume that any closed vessel is
pressurized until proven otherwise by use of the manual Safety
Test Valve.
12. Insert this SAFETY
ALERT in your Gaston County Operating and Maintenance Manual for
quick reference.